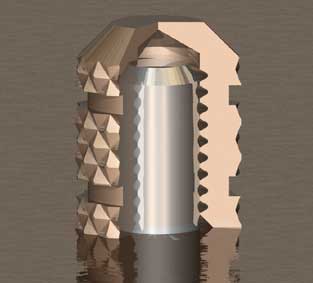
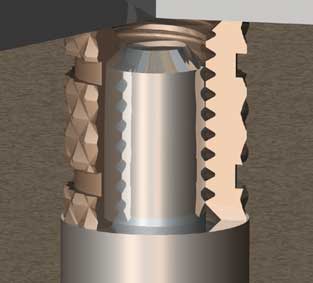
Technical advancement of traditional ‘mold in’ threaded inserts
Moulding-in for Thermoplastic and Thermoset materials
Tappex HiMould® inserts have become widely used for most types of thermoplastic and thermoset plastics as they are suitable for both injection and compression molding processes.
HiMould® range ‘generic’ insert features:
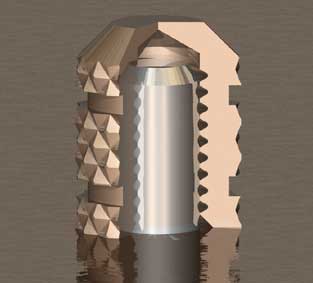
Type A
- Blind-ended design
- A standardised insert and pin design cutting down design time
- The open face is accurately machined at right angles to the axis of the insert
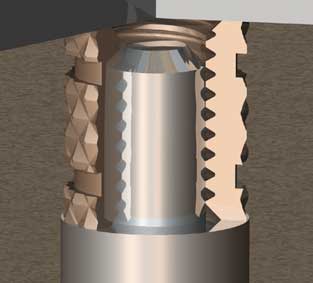
Type B
- Open-ended geometry
- A standardised insert and pin design cutting down design time
- It is possible to hold the length of the B type insert to +0.05mm/-0.05mm, to enable the tool to shut solid on the insert giving flash free threads
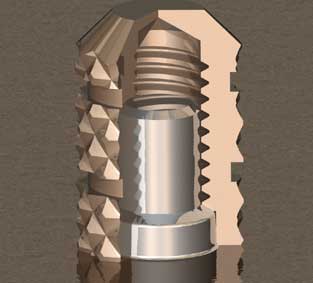
Type C
- Blind-ended geometry with additional counterbore feature; suitable also for vertically installed ‘core pins’, i.e. works well when located on the moving-top half of the mold tool as it offers better retention rather than just gravity or where inserts can easily become dislodged either before or during the molding process
- A longer length insert to cope with variation in bolt length and clamping thickness
- Excellent performance in foam materials also where flashing often occurs due to the searching nature of the plastic; insert incorporates extra counterbore feature in open-end; especially suitable for high pressure / low viscosity melts
HiMOULD® - TYPE A - 116M3
REACH/RoHS compliant as per the candidate list of substances of very high concern.
Finish: Self-Colour. Special finishes to customer requirements, at extra cost.
Description: The HiMould 'A' type insert for moulding-in, has an external diamond knurl form with two undercuts. The HiMould is dimensionally interchangeable with its' Yardley equivalent.
Application: This blind insert is designed to be installed onto a plain pin in the mould tool. The molten plastic flows around, and engages with, the external form during the moulding process. The shorter length over the Type C allows its use in areas where space is restricted. Provides excellent pullout performance and resistance to rotation.
Pin Design: The pin design and tolerance information is intended to indicate the dimensional requirements for satisfactory installation of the insert. They should not be specified for production tooling without prior consultation with our Application Engineering Department - we accept no responsibility should the use of this information without consultation result in product failure.Please call our application engineers for assistance +44 (0) 1789 206600
Installation: The Tappex HiMould type 'A' insert is designed to be used on a plain pin in the mould tool. It's manufactured with the internal thread produced to reamed bore tolerances. The open face is accurately machined at right angles to the axis of the insert. The dimensions of the tool pin allow for a slight interference fit between the pin and the internal thread of the insert, which holds it in place in the tool. The square face fits flush with the mould tool and eliminates flash.
Insert Design
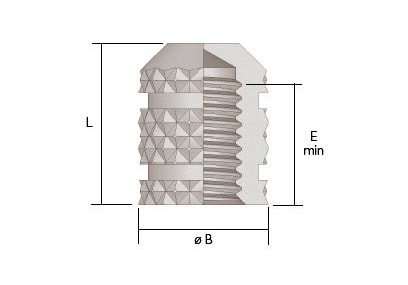
Bolt Engagement E (min): | 3.70 mm |
Dia (external) B (± 0.25): | 4.15 mm |
Length L (± 0.25): | 6.40 mm |
No. of Full Threads: | 6.80 mm |
Part No.: | 116M3 |
Pitch (internal): | 0.5 |
Thread Size: | M3 |
Pin Design
The following are downloads relating to the HiMould® range, although a downloads may also be applicable to other product ranges. General information can be found on our downloads page.
If you can’t find what you are looking for, why not try our chat facility where one of our helpful team can assist you or simply give us a ring on +44 (0) 1789 206600.
Tappex 2018 Brochure
Product brochure with overviews and descriptions of products.
Threaded Inserts for Plastics a ten point guide
Tappex Performance data of Inserts for Plastics in generic applications.
Tappex Performance data of Inserts for Plastics in generic applications.