Tappex Heat Inserter customised to manufacturing process resulting in cost and time savings
A local molding company, which makes interior components for the automotive industry, recently contacted us, having researched our Generation 3 multi-point Heat Installation tool.
They had an injection-molded component that required the post-mold insertion of 4 Tappex Multiserts. Our customers told us they are keen to use new and innovative equipment and develop new methods to constantly improve production, and we were able to help them achieve these goals while also increasing productivity and saving costs in the manufacturing process of this component.
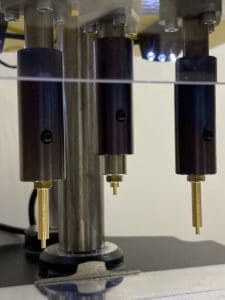
Our Heat Inserter has the ability to have multiple heat cartridges of different lengths
We were able to collaborate with their design engineers to offer tailored heat tip locations to match the customer’s own jig. The ability to install 4 inserts simultaneously will offer substantial time and cost savings over the previous single-point equipment and can easily be reconfigured for use with future projects.
Our Heat Inserter is also capable of holding heat cartridges of different lengths, which is very beneficial to the customer if they have multiple inserts to heat insert into the component at different heights.
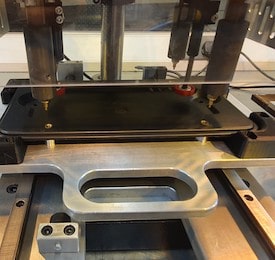
A custom-made jig allows for easy and repeatable positioning of the plastic moulded component
The machine was able to go directly into the production process, providing a plug-in solution adjacent to the moulding machine. Thread insert installation can now be completed by the operator within the moulding cycle time.